なぜ日本のものづくりは機能安全認証が苦手なのか?
日本企業が抱える潜在課題をエキスパートたちが語る
機能安全規格への対応が求められるのは、車載系だけではない。今後、産業機器や家電機器などの非車載系でも認証の取得が必須になる。ところが、非車載系は車載系に比べると機能安全認証の取得が難しいとされている。どうすれば、非車載系でも効率的かつ短期間で取得できるのか。その秘訣などをエキスパートたちに座談会形式で討論してもらった。
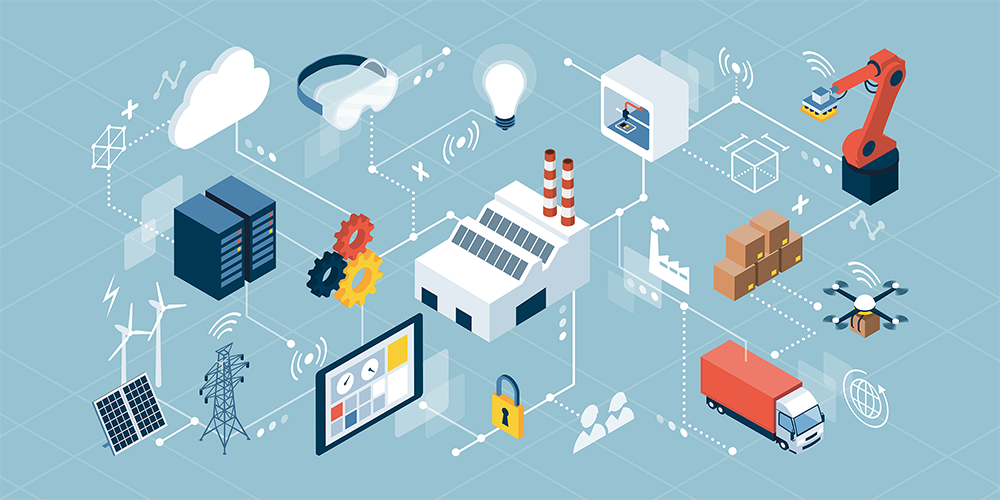
参加者は、機能安全認証の取得に向けたコンサルティング・サービスを提供するセーフティイノベーション(SIL)の斉藤進一氏、佐藤市太郎氏、高野明氏、安全通信のソリューションを提供するHMSインダストリアルネットワークスの伊東仁氏、コンパイラ・ベンダーであるIARシステムズの山田優氏である。なお、山田優氏は組み込み機器の機能安全に特化したエキスパート集団「FSEG(Functional Safety Expert Group)」の事務局も務めている。
いま、なぜ機能安全認証が必要なのでしょうか。
その理由を教えてください。また、機能安全認証を取得すれば、どのようなメリットが得られるのでしょうか。
伊東 いま当社では、「機能安全認証を取得したい」と相談に来られる顧客が増えています。理由は2つあります。1つは、顧客の顧客から機能安全への対応を求められていること。もう1つは、顧客のライバル企業が機能安全に対応した製品をすでに市場投入していることです。
後者の理由でいえば、人と同じ現場で動くロボット、つまり協働型ロボットの導入例が増えていることが影響しています。新型コロナウイルスの感染が拡大しており、作業現場の人員を減らしたいという要求が強い。それに対応するために協働型ロボットが必要になり、安全性を確保するため機能安全への対応が急務になっています。
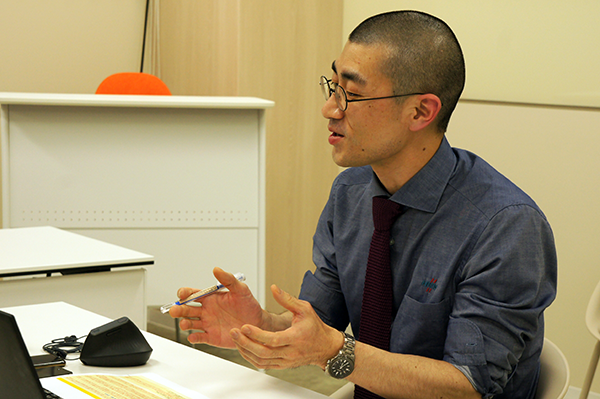
斉藤 私も、機能安全認証を必要とするケースは2つあると思います。1つは、部品メーカーが製品を収める完成品企業から機能安全への対応を求められるケースです。例えば、プレス機や工作機械などを欧州で販売する場合、機能安全認証の取得が必須です。そのため、完成品に使う部品を製造するメーカーに対して、機能安全認証の取得を依頼しているわけです。
もう1つのケースは国際規格への対応です。最近では建設機械に向けた機能安全規格「ISO19014」が制定されました。それに合わせて機能安全認証を取得したいという動きがあります。
佐藤 日本はWTO(国際貿易機関)に加盟しているので、国際規格を順守する義務があります。このため、国内全体で機能安全認証を取得する機運が高まっています。いまや車載機器や産業機器だけではありません。家電機器でもその動きがあります。
山田 私は3つの理由があると考えています。1つ目は、国内市場は縮小傾向にあり、内需ではもう、大きな拡大が見込めないことです。このため、どの国内メーカーも海外売上比率を高めることが最優先の経営課題です。ただ海外市場、特に欧州市場に進出する場合は、機能安全認証が高いハードルとして立ちはだかります。個人的な意見ですが、機能安全規格はドイツの産官学が連携して構築した一種の参入障壁のような意味合いがあるでしょう。最近では、欧州以外の市場でも当然のように機能安全の対応を求められるケースも多いと聞きます。つまり、海外市場で成功を収めるには、この障壁をクリアしなければなりません。
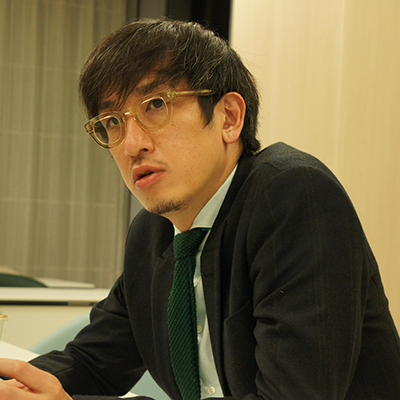
2つ目は、伊東さんもご指摘の通り、新型コロナウイルスの感染が拡大してニューノーマル(新しい生活様式)の時代に突入したことです。これからは人と人との接触を減らすため、人とロボットが協働して作業する場面が増えます。その際に、安全性をいかに担保するのか。国内のロボット関連メーカーにとって、機能安全認証を取得することは極めて重要になるでしょう。
3つ目は、ソフトウエア制御の広がりです。国内企業は、本質安全に対する取り組みは得意です。しかし現代社会は、ソフトウエア制御を使ってきめ細かな制御を実現することを優先させています。ソフトウエア制御を導入すれば潜在リスクが高まりますが、交通事故が起きる可能性があるからといって、車をすべてなくせという話にはなりません。リスクをゼロにするのではなく、社会が許容できるレベルまで抑える。その見返りとして大きなメリットを享受するという考え方がグローバル・スタンダードです。機能安全規格は、リスクとそれへの対応について社会全体でコンセンサスを得るスキームの1つであるわけです。
モーター制御の安全機能を例にとれば、電源供給を遮断するだけのSTO(Safe Torque Off)と、減速させた後に電源供給を遮断するSS1(Safe Stop 1)を比較すれば、後者の方がより多くのソフトウエア制御が必要になるでしょう。ただし、ここに機能安全認証を適用すれば、ソフトウエアによるきめ細かな制御が可能になり、生産性が向上する。こうした点が大きなメリットになります。
規格書を読んでも分からない
なぜ機能安全認証の取得は難しいのでしょうか。
伊東 最大の理由は、ノウハウや進め方をご存じないからだと思います。認証を一度取得した企業であれば、社内に一通り経験した人がいます。その人に聞けば、次の取得時は比較的スムーズに進むでしょう。しかし、認証の取得に初めて取り組む企業だと、経験者が社内にいません。特に当社が扱っている安全通信の分野は、経験者がより少ない。難題に遭遇したときに相談する人がおらず、暗礁に乗り上げてしまうわけです。経験者がいるか、いないか。これが認証取得時の難易度を決めることになります。 ただし、「経験がなければ、機能安全認証を取得できない」というわけではありません。国内企業には、これまで培ってきた品質管理の経験や考え方があります。これを活用できる。例えば、品質マネジメント・システム規格「ISO9001」で品質管理の仕組みをしっかり構築した企業であれば、認証取得時のハードルを下げられるはずです。
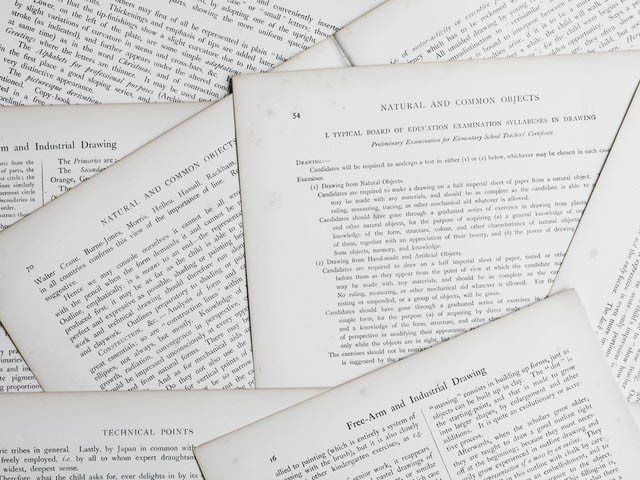
斉藤 認証の取得が難しい理由は2つあります。1つは、機能安全の規格書を読んでも、内容がピンとこないことです。恐らく、規格書を初めて見た人は、そこから何をすべきかを読み解けないでしょう。書かれていることは何となく理解できますが、何をすればいいのか分からない。そこでみんな悩んでしまいます。
もう1つは、規格書に書かれている内容を理解できても、どうすれば認証を取得できるかが分からないことです。よくよく規格書を読めば書いてあるのですが、全体的なシナリオまでは見えてこない。これで多くの人が行き詰まってしまいます。
機能安全に関する書籍は、かなりたくさん出版されています。そうした書籍を読めば、そうした困りごとを解決できるのでしょうか。
斉藤 現在、様々な解説書が出されています。これらの本は、機能安全の規格書の中身を理解する上で大変参考になります。しかし、いざ認証を取得しようとすると、そこで悩んでしまう。本を読んでも、「自分たちが開発する製品では実際に何をすべきか」まで落とし込めないからです。
山田 「機能安全の規格書は辞書」。これが私のイメージです。辞書があれば、きれいな文章を書けるわけではありません。しかも文章の書き方は、家族に向けて書くのか、上司に向けて書くのかなど、目的で大きく違ってきます。文章はすべて、辞書に載っている言葉だけで書けるのですが、目的による書き分け方までは説明していません。だから辞書を読んだだけでは、目的に適う文章が書けない。つまり規格書を読んだだけでは、認証を取得できないわけです。
高野 規格書には、具体的なサンプル、もしくはサンプルを作るガイドラインはまったく書かれていないんです。製品によって搭載する部材や部品が違うため、細かな適用方法は製品で異なります。従って、ほかの分野の例を参考にしても、すべてを解決できません。そこで悩んでしまうわけです。「Aの場合はこう、Bの場合はこう」。そういったサンプルやガイドラインが用意されていると導入しやすくなるはずです。
機能安全認証を新しい分野で取得する場合、何を参考にすればいいのでしょうか。もしくは、誰に聞けばいいのですか。
高野 社内に経験者がいる場合はその人に聞けばいいのですが、いない場合は、当社のようなコンサルティング会社に相談された方が良いと思います。
佐藤 機能安全認証は、自動車の運転免許取得に似ています。学科や法規は教科書で学べます。ブレーキやハンドルなどの場所や役割、自動車の構造、標識の意味など、一通り勉強します。しかし、これだけでは運転できない。実際に運転してみて技術やノウハウなどを身に付けなければなりません。このため多くの人は自動車教習所に通って、理論と実地の両方を学び、はじめて運転できるようになるわけです。当社のようなコンサルティング会社は、自動車教習所の役割を担います。
規格の対象は設計開発の手法や技法
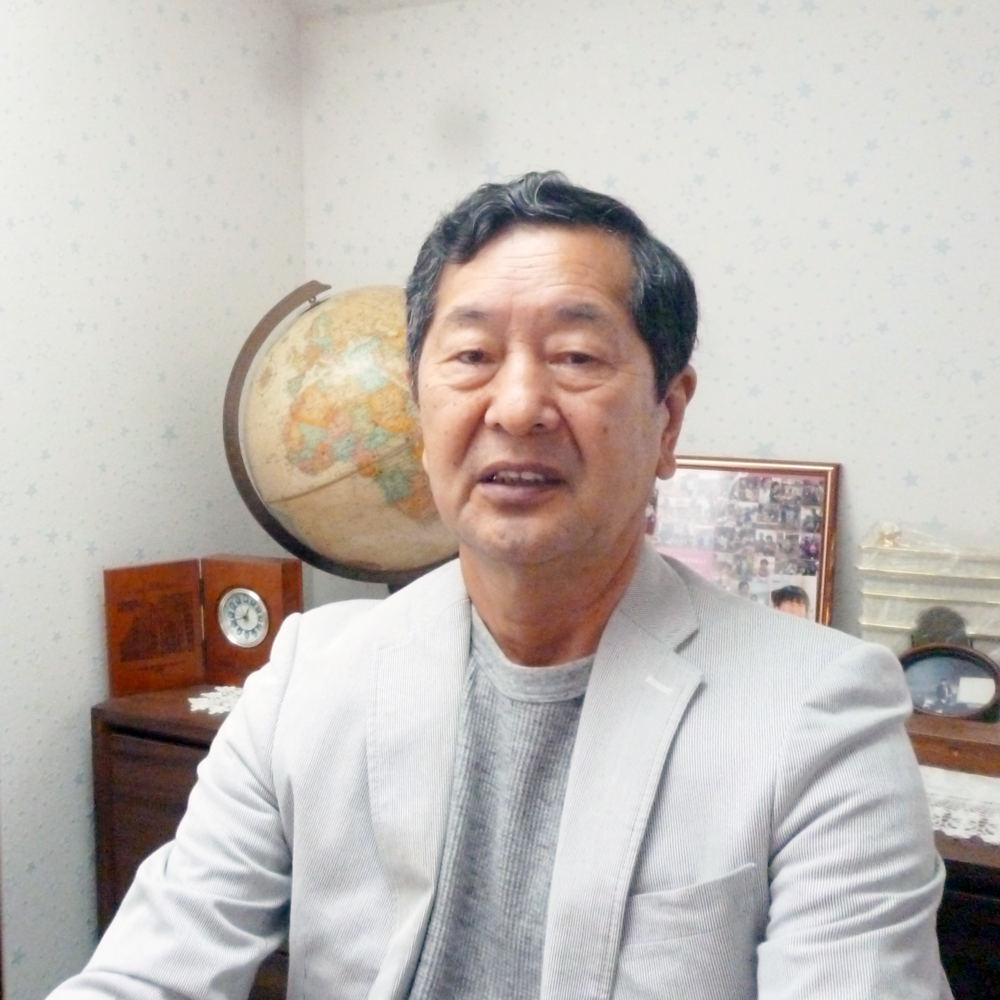
佐藤 なぜ機能安全認証の取得は難しいのか。そこに話を戻しましょう。一般的に製品を市場投入するには、様々な規格をクリアする必要があります。例えば、電源装置であれば、安全規格(ULなど)や不要輻射規格(EMCやFCCなど)を取得しなければなりません。まさに規格は多岐に渡っています。ただし、それらの規格はいずれも、製品を試験するためのものであり、規格書を読めば理解でき、実行できるものが多い。なぜならば規格書には「製品については、この試験項目とこのスペックを満足しなさい」ときちんと書いてあるからです。
ところが、機能安全の規格書には、設計開発の手法(ハードウエアの開発プロセス、ソフトウエア開発プロセス)や技法(設計技法、テスト技法)が含まれています。要するに機能安全規格は、「設計開発のやり方」を規格化しているわけです。「完成した製品はこのスペックを満足しなさい」だけではないのです。これが機能安全認証の取得を難しくしている最大の原因だと思います。
さらに、機能安全規格が設計開発の手法や技法を対象にしていること自体も、認証の取得を難しくしている原因の1つでしょう。国内には、設計開発に長年にわたって取り組んできた企業が多数あり、それぞれが設計開発手法を確立しています。ところが機能安全認証を取得するには、この手法を変えなければならない。ベテラン技術者ほど、規格に適合する開発手法に変えることに対して「難しい」と感じているはずです。
国内企業の設計開発現場では、設計開発に関する詳細資料を系統立ててドキュメントで残すという作業が疎かになっていることが多々あります。機能安全規格では、設計開発のエビデンス(証拠)をドキュメントとして残すことを規格化しています。これまでの国内企業の仕事の進め方から考えれば、かなり抵抗があるはずです。従来の仕事のやり方とマッチしない。だから、多くの人が機能安全認証の取得で苦労するのでしょう。
山田 私は、機能安全認証の取得が難しい理由は3つあると感じています。1つは、認証取得に関するノウハウが世の中に流出しないことです。車載系以外、つまり非車載系は第三者認証であり、例えば、独TUVなどの認証機関にお墨付きをもらわないと認証を取得できません。認証機関は、グローバルで様々な企業を見ています。恐らく、最適もしくは最短の取得方法を知っているはずです。しかし、認証機関は、認証取得に向けた答えは教えてくれない。教えてしまうと、ある企業のノウハウを競合他社に漏らしてしまうことになるので、立場上教えられません。もちろん機能安全認証を取得した企業もノウハウを外部に公開しないでしょう。つまり、どこからも認証取得に関するノウハウが表に出てこない。
2つ目と3つ目の理由はいずれも、日本特有に文化に起因するものです。まず2つ目の理由ですが、国内企業は自前主義にこだわることです。あまりにもこだわるため、機能安全に関する知識やノウハウが乏しくても、コンサルタントやFSEGといった社外の力を借りることにどうしても躊躇してしまう。結局、一度火傷しないと、社外に声を掛けられない。機能安全認証自体は、ものづくり企業のコアコンピンタンスではありません。「餅は餅屋」と割り切って専門企業に任せて、社内の優秀なリソースはコア技術に集中させる選択が必要でしょう。
3つ目の理由は、グローバルなコミュニケーションは日本とは異なることです。日本人はテキストで網羅的に説明するのが得意ですが、海外では図などを多用して全体像の説明から入ります。機能安全認証とは説明することでもあり、認証機関は言語が違う欧州人(主にドイツ人)です。このため日本特有のテキスト・ベースの説明だけだとなかなか伝わらない。やはり、図を上手に使って説明するコミュニケーションを取り入れたり、説明自体を工夫したりすることが必要でしょう。
業界一丸となって取り組む車載系
機能安全への取り組みについては、車載系と非車載系の違いはどこにあるのでしょうか。その差について教えて下さい。
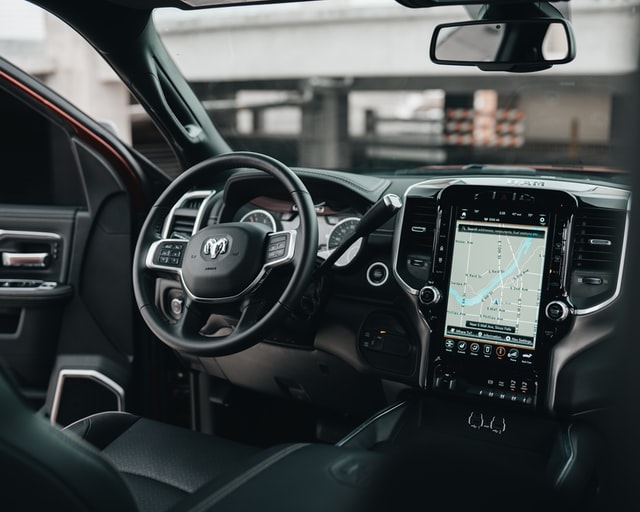
伊東 車載系の機能安全には、「ISO26262」という規格があります。これに準拠する形で、大手自動車メーカーが先導しながら、機能安全認証の取得に向かって業界一丸となって動いています。非車載系の機能安全には、基本規格として「IEC61508」があり、そのほか製品ごとにそれぞれ規格が用意されています。
このように規格一つとっても、車載系と非車載系では違います。従って、両者の比較はとても難しいのですが、ISO26262の要求事項の方がより明確化されている上に、先行事例がたくさんあります。このため、これから新しく取得しようとする企業が進めやすい環境が整っているといえます。
一方で非車載系は、企業ごとの取り組みに大きな差があったり、ノウハウを企業内部に抱え込んだりするところが多いのが実情です。非車載系で機能安全規格に準拠しようとすると、かなりハードルが高い状況です。例えば、モータードライブやエンコーダを機能安全規格に準拠させるには、どう作り込めばいいのか。そのノウハウを各企業がそれぞれ抱え込んでいるため、同じ分野に取り組む企業にもかかわらず、どこもまっさらの状況から始めないといけません。
どこかの企業がいずれノウハウを公開し、近い将来、ノウハウが共有されるようになるのでしょうか。状況が改善されるようになるのか。
伊東 いや、そういう状況にはならないでしょう。みんな同じ道を通って、同じノウハウを蓄えて、気がついたらいつの間にか同じノウハウを共有していたという状況になると思います。
高野 自動車は、安全に対する要求レベルがすごく高い。とにかく止めればいいわけではありません。安全に、事故が起こらないように自動制御しなければなりません。安全度水準(ASIL:Automotive Safety Integrity Level)はDの取得が大前提です。このため車載系では、安全に対する取り組みが先行しています。つまり車載系で確立された安全技術が非車載系(産業分野など)に降りてくるという印象です。実際に、自動車での取り組みは先進的であるため、観察しているだけでも勉強になります。
例えば、半導体技術の進化を背景に1チップにCPUコアを4個も6個も集積できるようになったため、自動車ではこのチップを使った集中処理システムへの移行が始まっています。従来は、50個や60個ものマイコンを使って分散処理するのが当たり前でしたが、1つのマイコンが大きくなることで、マイコンの使用個数を減らす方向にあるわけです。この考え方を非車載系に適用すれば、安全度水準を高められるはずです。
車載系で参考になる取り組みはもう1つあります。プログラム・コードを自動生成する技術の導入です。例えば、米MathWorks社のツール「MATLAB」を使えば、コンピュータ上でブロックを描くだけで、プログラム・コードを自動生成できます。この技術を非車載系で導入すれば、省力化に加えて、安全度水準を高められるでしょう。
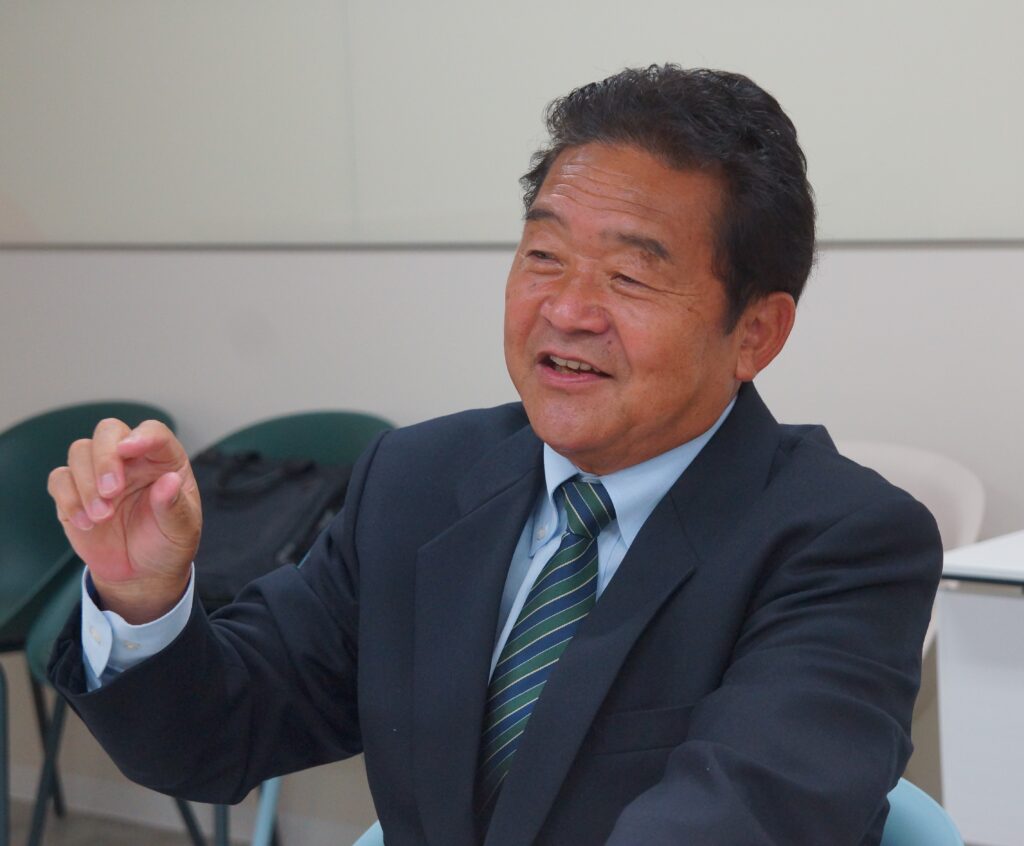
山田 当社でも、グラフィカルにステートマシンを設計し、プログラム・コードを自動生成するツール「IAR Visual State」を製品化しています。すでに海外や国内の大手車載ティア1(Tier1)をはじめとする機能安全に敏感な企業に、かなりのライセンス数を採用してもらっています。
非車載系は第三者認証
斉藤 車載系で機能安全への取り組みがなぜ進んでいるのか。それは自動車業界における一連の流れに理由があると思います。車載向けの国際規格であるISO26262が発行され、それに対して国内の自動車メーカーが一斉に取り組むことを表明し、車載部品メーカーが認証機関を動かして車載部品の故障率を規定してもらい、自動車メーカーがそれに準拠するように車載部品メーカーに一斉に要求を出した。こうした一連の動きがあったからこそ、車載系での取り組みが一気に進んだわけです。
もともと機能安全規格は、「電気・電子・プログラマブル電子(Electrical・Electronic・Programmable Electronic)」が対象です。従って自動車では、ブレーキやハンドル、ステアリングなどの制御装置が対象になる。こうした制御装置を製造する車載部品メーカーを巻き込んで一気に広まったわけです。
一方、非車載系には工作機械やプレス機などが含まれますが、いずれも業界全体を対象とする動きはありません。各企業が独自に取り組んでいます。つまり、非車載系の完成品企業が欧州に製品を輸出するため、機能安全規格への準拠が必要となり、採用する部品を製造するメーカーだけに理由を説明して機能安全規格に準拠してもらっているわけです。依頼を受けたメーカー以外は無関係です。
佐藤 安全な自動車は現代社会の大きなトレンドです。より安全性の高い自動車を開発すれば、売上高が伸びます。当然、自動車メーカーの経営層は、安全な自動車の開発を指示しているはず。従って、自動車業界は、機能安全への対応を含めた安全な自動車の開発を競っているわけです。
それでは非車載系はどうか。多くの業界ではまだ、安全性をキーワードにした開発競争は遅々として進んでいない状況だと思います。こうした業界でも、安全性を競う仕掛けを作ることができれば、車載系のように機能安全に対する取り組みが一気に進む可能性があるでしょう。
高野 自動車には、必ず人間が乗ります。そのためリスクはどうしても大きくなる。しかし、工作機械などは基本的に無人で動きます。もちろん段取りや保守といった作業時は人間が介在しますので、ある程度リスクは高まります。ただし、リスクの程度は自動車に比べればかなり低い。このため車載系の方が非車載系よりも、機能安全規格の対応で進んでいるのはある程度納得できます
山田 車載系と非車載系の差を考えたとき、一番大きいのはどの自動車もほぼ同じような部品で作られていることです。メーカーや車種が違ってもハンドルやブレーキ、ステアリング、ヘッドライトなど、使用する部品はほぼ同じ。しかし非車載系は、メーカーや製品によって使用する部品はまちまちです。半導体チップやプログラム・コード量も製品で大きく違う。恐らく、車載系の機能安全への取り組みが進んでいるのは、自動車はほぼ同じ部品、ほぼ同じ設計で作られており、知見やノウハウを共有しやすいからでしょう。
車載系と非車載系には、大きな差がもう1つあります。この差は、是非とも強調しておきたい。それは、車載系は自己宣言ですが、非車載系は第三者認証が一般的であることです。車載系の場合は、すごく雑に言えば自動車メーカー(OEM)がすべてを判断するため、全体のシステムに対して部分的に関与する車載部品メーカー(Tierメーカー)が機能安全認証に関して工夫したり、交渉したりする余地は実は少ない。しかし非車載系であれば、メーカー自身が開発したシステムを第三者である認証機関に説明する流れになるため、工夫次第で競争力や効率を高めることが可能です。この違いはかなり大きい。従って、「車載系の方が機能安全への取り組みで先行している」というメッセージの出し方は誤解を生むケースがあるかもしれません。状況がまったく違うからです。
「車載系が先行し、非車載は遅れている」という議論はあまり意味を成さないということですか。
山田 意味がないとはいいませんが、単純に比較できないので、この議論を深めてもあまり有益な結論は得られないでしょう。必要以上に自動車業界を意識すると、非車載系の取り組みにおいて本質を見誤り、競争力を落としてしまうのではないか。その点を危惧します。
担当者が代わると苦労する
機能安全認証の取得において、具体的な成功例とトラブル事例を教えて下さい。
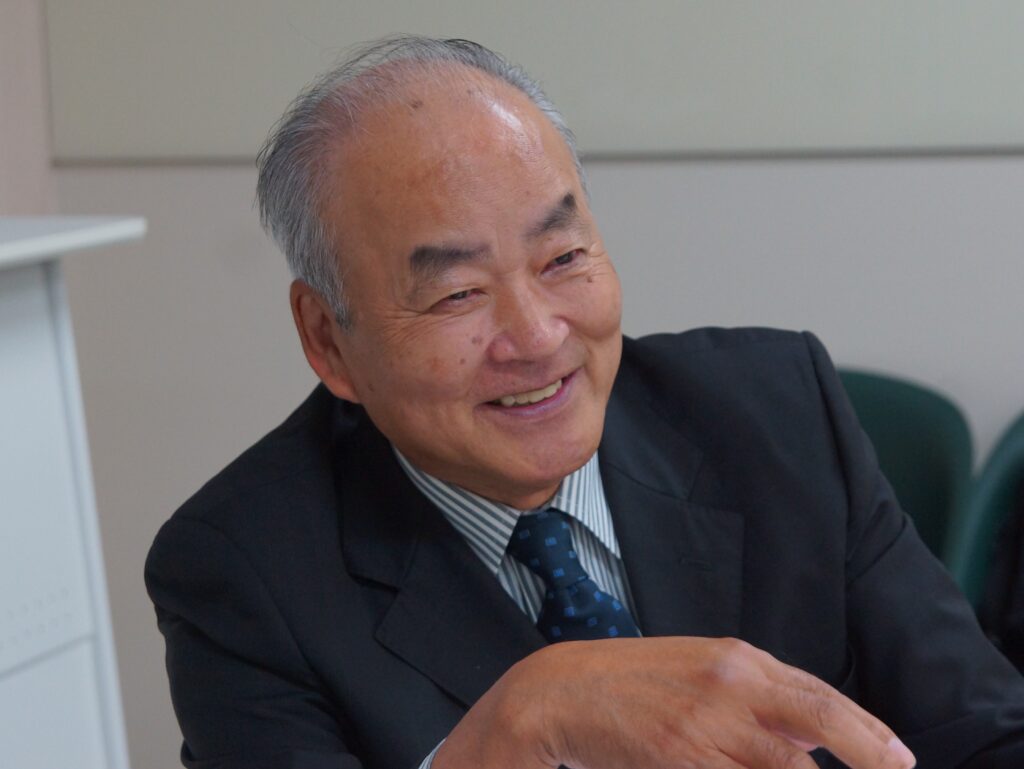
斉藤 機能安全認証をうまく取得できた企業は、決まって2つの条件がそろっています。1つは、開発体制がしっかりしていること。もう1つは、トップ・マネージメント層の理解があることです。トップ・マネージメント層が「いつまでに取得するんだ」という意思を示し、これを企業の末端まで徹底することが必要です。徹底されていれば、8〜9割はうまくいくはずです。逆に徹底されていなければ、途中で頓挫してしまうでしょう。さらに付け加えれば、認証機関とコンサルタント会社の間に入る企業担当者がうまく機能することも大切です。
逆に苦労するのは、途中で開発担当者が交代したり、別の案件との掛け持ちで十分な開発時間が確保できなかったりするケースです。技術的な面よりも、開発体制の影響の方が大きいです。
伊東 斉藤さんに質問があります。当社では、顧客を対象とした機能安全セミナーを開催しているのですが、その中で「機能安全に初めて取り組む際は、なるべく小規模な安全機能を対象にしましょう」と呼び掛けています。実際のところ、開発経験が豊富な企業などで、自信があるため複雑な安全機能から手掛けてしまって大変な目に遭ったというケースを見たことがありますか。
斉藤 実際に、3つの安全機能を同時に開発したいという顧客がありました。ただ、その際には「現行の開発体制で同時進行させると無理が生じます」と諭し、3つの安全機能を順番で開発するスケジュールを立てました。まずは認証を取得する範囲を明確にすることがとても大事です。それがあやふやだと混乱してしまい、より多くの時間がかかってしまうことになります。
伊東 私の経験では、2個の安全機能を同時に開発すると、1個だけを開発する場合に比べて、その複雑性は単純に2倍ではなく、それ以上に跳ね上がります。このため、「まずは小規模な安全機能から開発しましょう」と提案しています。
斉藤 2倍ではなくそれ以上。それはその通りです。ただ最初から3つの安全機能を開発する予定であれば、それぞれの安全機能間のインターフェースを最初に決めておくことが重要です。
それぞれの安全機能を別チームで開発すれば、安全機能が1個から2個に増えても、作業量は2倍ではないのでしょうか。
伊東 それぞれの安全機能の間には、相互作用が発生する可能性があります。これを考えながら開発しなければならない。開発する安全機能が増えれば増えるほど、考慮すべき点が多くなります。あらゆる相互作用を考慮して開発するか、あるいは相互作用が発生しないような仕組みを考えるか。いずれにしても単純に2倍にはなりません。
セーフティイノベーション(SIL)がコンサルタントとして参加することで、成功に導いた事例を紹介してください。
斉藤 顧客からはたびたび、「どうやって作業を進めたらいいか分からない」と言われます。そこで当社では、各種テンプレートを用意しています。これに必要事項を書き入れていけば、認証機関が必要とする情報を漏れなく記載できます。実際には、顧客と当社が一緒になってテンプレートをベースに必要なドキュメントを作成し、それを認証機関に提出しています。 認証機関から直接、顧客のところに質問が届くケースもあります。その質問を顧客が十分に理解できない場合は、当社が間に入って質問内容を理解し、顧客と一緒に回答内容を考えて認証機関に返答しています。つまり、当社の業務は顧客と認証機関のコミュニケーションのギャップを埋めることにあります。
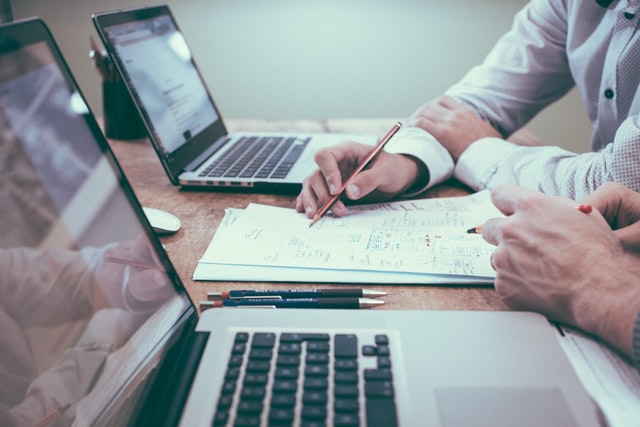
ものづくり企業の競争力を高める
FSEGを立ち上げた目的を教えて下さい。
山田 FSEGは2019年1月を立ち上げました。その最初の定例会で、参加企業の担当者と話し合って、「FSEGの2つの目的」を決めました。1つは、日本のものづくりの競争力を高めること。もう1つは、ビジネスにつながる活動にこだわることです。事務局としては、情報交換だけで終わってしまうワーキング・グループのような活動は明確に避けるようにしています。FSEGを利用する顧客のビジネスにつなげたいですし、FSEGの参加企業の利益にもつなげたい。こうした考え方に基づいてFSEGは活動しています。
FSEGを利用するユーザーが享受できるメリットは何でしょうか。
山田 当社はコンパイラ・ベンダーですが、ユーザーのところに行けばコンパイラ以外のことも聞かれます。困っているユーザーは助けたいのですが、自社製品だけではどうにもできない。そこで、機能安全規格に関わる企業が集まって作った団体がFSEGです。
伊東 ユーザーからしてみれば、複数の会社にコンタクトしなくても、FSEGに連絡すればすべて完結する。1つの窓口だけで様々なサポートを受けられる。「機能安全エコシステム」と呼べるでしょう。この点がユーザーから見たときの最大のメリットといえます。
実際、FSEGではどのような活動をしていますか。

山田 例えば、最近ではマネージメント層や経営層に向けた個別相談会を開催しています。機能安全の経営に関わる課題を解決することは非常に重要です。例えば、機能安全規格を取得して海外市場に進出することを決定する場合、取得にかかる工数や難易度が分からなければ、実際の作業に取りかかれません。さらにマネージメント/経営層は機能安全規格の取得に向けた判断材料を欲しがっています。FSEGはそうした材料を提供していきます。
このほか無償サービスとして、セミナーの開催やホワイトペーパーの提供などにも取り組んでいます。さらに有償サービスですが、1日のトレーニングや、1〜数週間のコンサルティングなども提供しており、工数のイメージや見積もりの作成までをお手伝いしているケースもあります。もちろん、最初から機能安全認証を取得することが決まっているプロジェクトであれば、セーフティイノベーション(SIL)のようなコンサルティング会社が最初から最後まで二人三脚で寄り添って作業を進めることも可能です。
様々なものづくり企業が、機能安全認証の取得に向けて異なるフェーズで悩みを抱えています。FSEGは、そうした各フェーズの悩みに対して、的確な判断を下すために必要な材料を提供し、サポートを提供できるメンバー企業がそろっています。
FSEG自体は営利団体なのでしょうか。
山田 顧客である国内製造業、およびFSEG参加企業のビジネスにつなげるためにFSEGは活動しています。団体として利益を上げるわけではありません。国内のものづくり企業が機能安全に関わるプロジェクトを前に進めれば、組込み業界全体の利益として返ってきます。その際、FSEGの参加企業の新しいビジネス獲得につながるわけです。排他的なビジネスを展開するつもりはありません。
正直なところ、FSEGのような機能安全認証取得のエコシステムに関わる国内企業は非常に少なく、顧客が抱える潜在課題に対しては数がまだ足りてないという認識です。一方で、顧客側は潜在課題に気付いていないケースが多い。今は、顧客となる国内のものづくり企業が、機能安全に関する潜在課題を認識し、スピード感ある意思決定と開発を推し進めて国際競争力を高めていくべきフェーズです。国内のものづくり企業がグルーバル市場で活躍できれば、FSEGのような団体が増えて、一緒に成長していく流れを作れるでしょう。実際に、2019年に小さな規模で始まったFSEGですが、現在ではSTマイクロエレクトロニクス、ルネサスエレクトロニクス、日本テキサス・インスツルメンツといった大手半導体メーカーが正式に加入しています。今後も、こうした動きが業界内に広がっていくことを期待しています。
FSEGのサポートを受ける方法はどうしたらいいでしょうか。
山田 相談会をご用意していますので、必要事項を書き込んで頂ければ個別に相談会を設定させて頂きます。相談会では、実際に抱えている課題を聞き、その課題解決に最適なメンバーを紹介します。例えば、設計開発で困っていればセーフティイノベーション(SIL)を、安全通信で悩んでいればHMSインダストリアルネットワークスやインターファクトリーパートナーズ(IFP)を、解析/テスト・ツールであればテクマトリックスを、受託開発であればグレープシステムやエヌエスピージャパン(NSPJ)を、コンパイラ/デバッガの課題を抱えていればIARシステムズを紹介するといった具合です。
相談会は、初回(1〜2時間程度)は無料です。その後、例えばセーフティイノベーション(SIL)のコンサルティングを受ければ、費用が発生するという仕組みです。
今回の座談会参加企業

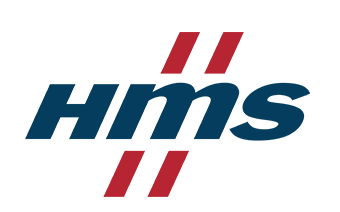
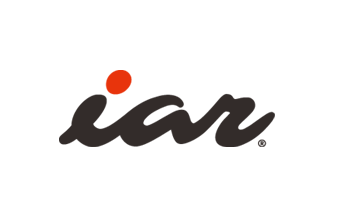